In a combination of three of
its subsidiary operations, the
Grindrod group has devised a
highly cost-efficient means of
transporting major consignments
of imported malt to its destination
at Sedibeng Brewery in Klip
Rivier in southern Gauteng.
“It was an effort combining
innovation and sustained cooperation
between three Grindrod
businesses, to get closer to meeting
the client’s needs,” said Adriaan
van Dyk, national line manager at
King & Sons and the originator of
the new plan.
Until now, the Grindrod
companies, King & Sons and
Grindrod Intermodal, have played
a traditional role in the import of
malt from France and Belgium via
the port of Antwerp, and carried
to Durban by Maritime Carrier
Shipping.
The cargoes are shipped and
transported to Durban in six-metre
containers, and/or 1.25 metric
tonne mini-bulk bags as breakbulk
parcels.
The containers are then railed
to Grindrod Intermodal Kazerne
depot and transferred to road
tipper trucks for delivery to site
as and when required. The big
bags are warehoused in Durban
and transported to Sedibeng
Brewery by road, on request of the
customer.
“We are currently in the pilot
phase of a project, which involves
using 12m containers that have
had hatches installed in the top,”
Van Dyk told FTW.
The containers are transported
to the vessel side on a flatbed
truck where they are loaded with
bulk malt via grab discharge into
gravity hoppers. Then the vehicles
pass through a weighbridge and
the containers are stacked fivehigh
at Grindrod Intermodal’s
Bremen Road depot.
When the brewery calls for its
malt, the container is lifted onto a
specially made tipping frame. One
end is raised and, as it vibrates,
the malt flows into a 40-cubic
metre bulk side-tipper truck, where
the bins have been completely
cleaned. They are then covered
securely, and the load is taken
by Grindrod Logistics’ dry bulk
trucks to the brewery.
There, the load is tipped into bins
which have been specially designed
to receive the malt directly from the
side-tipper road trucks. These bins
are then placed onto a tipping frame
by fork-truck on site. The malt is
then tipped into the intake facility at
the brewery’s conveyor system – to
be stored in its silos awaiting the
brewing process.
“The demonstration was a
success and was positively
received,” said Van Dyk. “It is an
example of how, by adapting to
the specific needs of the client,
integrated Grindrod companies in
the supply chain can add value to
our clients’ operations, and thus
secure future orders.”
Grindrod develops innovative logistics option for malt imports
10 Jun 2011 - by Alan Peat
0 Comments
Durban 2011
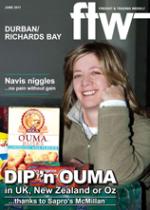
10 Jun 2011
10 Jun 2011
10 Jun 2011
10 Jun 2011
10 Jun 2011
10 Jun 2011
10 Jun 2011
10 Jun 2011
Border Beat
27 Jan 2025
Featured Jobs
New
New